THANK YOU FOR SUBSCRIBING

Unitechnology Co., Ltd.: Resolute in its Quality-First Approach to Technology

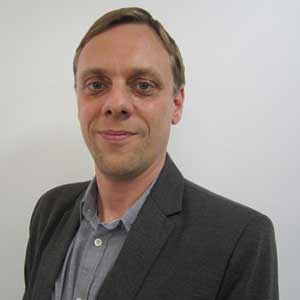
Candy manufacturers have valid reasons to resort to such tactics. For starters, convenience stores do not feature the same product for long, as it goes against their strategy and orientation. Secondly, confectionery brands are looking to reduce overhead costs by implementing more automation in their factories—and achieving this is impossible through conventional methods.
This is where Unitechnology, a provider of food and beverage technology solutions, is gaining traction. By calling upon the revolutionary product Coaterow, a next-generation coating machine, Unitechnology enables confectionery manufacturers to constantly reinvent their products and stay a step ahead of the curve.
Besides driving increased and factual production improvements, Coaterow has also succeeded in replacing the classic revolving pan. With the conventional revolving pan method, brands relied heavily on skilled workers to achieve the desired coating quality. In fact, the appearance of the coating often varied depending upon the quality of the workers.
Now, compare that to Coaterow, which comes with a unique centrifugal disk. Since Coaterow is integrated with software, candy manufacturers can simply call upon the program to ensure the coating process commences accordingly. The machine, while ensuring that every coating step is undertaken chronologically, delivers uniform quality each time. “With the conventional pan method, only the drum rotates, and the center disk remains statutory. Our centrifugal disk ensures both drum and center disk rotate, ensuring faster production times and superior quality with less maintenance,” says Steven Roelandts, General Manager of Unitechnology.
Furthermore, the HACCP-certified Coaterow is renowned for its long shelf-life, compactness, and user-friendliness. The parts can be easily disassembled for cleaning, and the tilted movement of the coating tank simplifies the process of charging the machine.
The infinite benefits of Coaterow can be found in several use cases. Recently, a soft candy manufacturer reduced its production facility from four conventional coating machines to just one Coaterow, reducing overhead costs in the process. In another example, a client succeeded in restructuring a cubic-shaped chocolate into a ball-shaped candy.
We do not go for second-grade technologies with lesser quality as we constantly strive to improve the production output and quality for our customers
After undergoing an initial test phase, the client bypassed two production processes and managed to launch the new product in record time. Roelandts notes, “After acquiring the step-by-step process recipe, the client stored it into the PLC, and commenced production. They got the desired ball-shaped candy.”
In the aftermath of the second use case, Unitechnology took the results to other confectionary companies. One specific client wanted to re-shape a round candy to a square candy. Again, Unitechnology established the correct step-by-step recipe during the trial phase and integrated the same into the client’s manufacturing process. The client succeeded in not only getting the desired product but reduced its volume of KGS coating materials and fastened the production time.
Coaterow is an illustration of Unitechnology’s commitment to adopting only cutting-edge technology, which is essential to upholding quality in the food and beverage sector. Roelandts elaborates, “We do not go for second-grade technologies with lesser quality as we constantly strive to improve the production output and quality for our customers.”
Unitechnology is also cognizant of its role in giving back to the environment. It has partnered with Chorushome to develop Biodegradable Additive Technology (BAT) that provides an additive to ensure complete biodegradation of plastics used by manufacturers of kitchenware utensils, F&B and pharmaceutical packaging. BAT is unique in that its additive mixes only at 1 percent of the plastic packaging during production, without affecting the strength and lifecycle of the plastic.
The additive only reacts at a biological active environment, which allows formation of biofilm in the absence of oxygen (i.e., Landfill).
“In Southeast Asia, especially, too much plastic is dumped into the landfills. This project is my personal baby, and I’m really committed to it,” adds Roelandts.
A bright future awaits Unitechnology, which plans to continue to abide by its “crossover” philosophy that sowed the seeds of the company in 2009—when founders Yasumasa Kondo and Katsuhiro Seki aligned their varying manufacturing and technological competencies under one umbrella. Even today, Unitechnology “crosses over” by supporting and seeking global suppliers for import into Japan and APAC, as well as supporting Japanese manufacturers with export sales and project integration across the world. “Based on our ‘crossover’ concept, the products within our business units are extremely wide-ranging,” adds Roelandts.
Forging ahead, Unitechnology won’t leave any stone unturned in serving customers. Although based in Japan, members of Team Unitechnology constantly travel to various parts of the globe to meet customers, understand their requirements, and perform feasibility assessments, before technology onboarding. The company does not believe in “sales via email or phone” and also provides post-deployment maintenance support. “Attention to detail and personal care is very integral to us, it is ingrained in the Japanese culture, and we take pride in it,” concludes Roelandts.

I agree We use cookies on this website to enhance your user experience. By clicking any link on this page you are giving your consent for us to set cookies. More info