THANK YOU FOR SUBSCRIBING
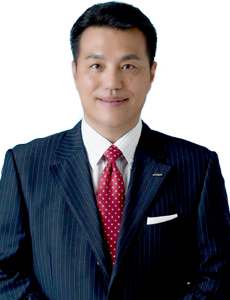
To solve these pain points, OMRON Corporation—a global leader in industrial automation—has launched its revolutionary Light Convergent Reflective Sensor “B5W-LB series” that combines four types of aspherical lenses and realizes stable detection with wide sensing range regardless of colors and materials such as shiny, black, and transparent surface. By adopting the “B5W-LB series,” factory manufacturing facilities are no longer affected by the change of object color and/or material and have significantly reduced the number of sensor-related malfunctions. The sensors, which can be embedded across a range of industrial equipment, ensure a wide detection range and allow for stable detection even if product positions vary.
"The aim is not to create a workplace where people can slack off, but to create an environment where everyone can work comfortably and feel motivated by their work"
This latest innovation is another example of OMRON’s determination to actively promote, research, and develop solutions to realize automation for various applications with sensors. OMRON’s award-winning sensing components don’t just detect, measure, analyze, and process various changes that occur on production sites, but also contribute to predicting and preventing future events (such as factory mishaps and accidents). Besides fiber sensors, proximity sensors, and vision sensors, OMRON offers a wide range of photoelectric sensors that are specifically designed to detect photo-optical workpieces. Some photoelectric sensors can be classified as diffuse-reflective, through-beam, retro-reflective, and distance-settable. OMRON’s comprehensive sensor suite also includes a range of liquid leakage sensors such as sensing bands, point sensors, chemical-resistance sensors, and sensors resistant to high temperatures. They are widely used in semiconductor production equipment and clean rooms. OMRON’s sensors can also be embedded with amplifiers or used with external amplifiers.
Engineering Smart Factories for Innovators
OMRON’s sensors are currently utilized in the most cutting-edge smart factories across the world. In recent years, many manufacturers are accelerating their efforts to transition to smart factories. However, a number of them are encountering obstacles such as the collection of data, and more importantly, developing the infrastructure for the accumulation of this data.
Embedded with self-navigation software, OMRON’s mobile robots can safely move, avoid obstacles and people
Foreseeing these data-related challenges a decade ago, AISIN AW Co., Ltd.— one of the world’s largest manufacturers of automobile parts—developed a data collection environment at its Okazaki Plant, with hopes of achieving favorable results in automation by leveraging automated guided vehicles (AGV), robotics, and AI.
After developing a “GPI (Global Product Line Information) Grid System”, or an information infrastructure, AISIN AW knew it was time to bring about automation and autonomy in their factories by leveraging robots and AGV. In 2016, AISIN AW chose OMRON as its partner to implement smart, automated, and autonomous factories. “We had already collaborated with OMRON through co-developing the high-speed automated X-ray CT inspection system. We started considering the introduction of robots to take a further step forward with automation. At that time, OMRON was also entering the robotics industry, and I felt that our goals were in line with each other,” says Osamu Yamato of AISIN AW.
A few years since partnering with OMRON, AISIN AW continues to evolve its smart factories, with a stronger emphasis on the design phase prior to production. OMRO is helping ASIN AW develop its own system to simulate operating conditions of production lines in a virtual environment. As a result, AISIN AW will be able to experiment with new ideas that could solve problems in the production line without actually implementing the ideas. Kunihiro Yamada of AISIN AW touches upon the collaborative relationship with OMRON, and the joint vision they share for the future of smart factories. “The aim is not to create a workplace where people can slack off but to create an environment where everyone can work comfortably and feel motivated by their work. Letting robots do boring manual tasks and having people work in fields where they can exercise their creativity and feel motivated—that is the sort of environment we wish to create,” says Yamada.
Factory Harmony with OMRON Robots
AISIN AW’s Okazaki Plant is just one of the many breeding grounds where OMRON is able to showcase what it refers to as the “manufacturing floor of the near-future.” While a number of its automation solutions and robots have already found wide application, the company is constantly dabbling in new ideas. Recently, at the CES 2019—a global convention for the world’s topmost business leaders and pioneering thinkers—OMRON showcased its next set of machines and robots that support the creation of “harmony between humans and machines.”
Some of these machines (currently in developmental stages) include mobile robots, laser markers, pick & place robots, and collaborative robots. The mobile robots are self-navigating Autonomous Intelligent Vehicles (AIVs) that can carry loads of up to 300 lbs, transport magnets and boxes to-and-fro from the production line, and perform other tasks within OMRON’s Factory Harmony Area. Embedded with self-navigation software, OMRON’s mobile robots can safely move, avoid obstacles and people. Meanwhile, the laser markers achieve high-speed and high-accuracy to deliver quality control and identification for factories. By recognizing the edges of objects, OMRON’s laser markers can accurately print information with a designated space, self-monitor the tools that it uses, and even detect shapes when objects have limited flat surfaces. The laser marker can mark a range of surfaces, including stainless steel, plastics, and other metals.
Meanwhile, OMRON’s pick & place robots recognize objects, picks them up and places them down in the desired configuration. Since they are built-in with AI, the robots are able to increase accuracy as and when humans suggest improvements.
Besides showcasing its Factory Harmony Area at CES 2019, OMRON introduced FORPHEUS, a robot table tennis tutor that embodies the world of “harmony” where machines can bring out human ability. While the two were showcased in separate booths, OMRON acknowledged that while FORPHEUS is “the theory,” Factory Harmony Area is “the application.” In other words, the various technologies in FORPHEUS are optimized and adapted for automation purposes in the Factory Harmony Area.
The name FORPHEUS comes from “Future OMRON Robotics Technology for Exploring Possibility of Harmonized Automation with SINIC theoretics”. FORPHEUS is also a combination of “For” and “ORPHEUS (a bard in Greek mythology as a symbol of human creativity)”, representing OMRON’s outlook of maximizing human creativity and possibility.
FORPHEUS, just like every other OMRON-designed robot, is engineered based on OMRON’s assumption of a three-step relationship between humans and machines. While the first stage is one of “replacement” by machines of tasks delegated by humans, the second stage is “collaboration” between the two parties. The second stage can already be found in several use cases such as the production line where humans and robots work together, or even OMRON’s collision-prevention technology that supports the company’s vision of a collision-free mobile society.
The third stage—which entails “harmony” between humans and machines to extend human capabilities—is where OMRON intends to get to. Through FORPHEUS, OMRON wishes to firmly establish a relationship between mankind and machines that can transcend the future.
Encouraging Woman Leaders
FORPHEUS is clearly determined to drive integration and harmony between humans and machines. However, industrial automation pioneers are equally focused on developing the next generation of leaders. With an aim to be an organization that encourages ideation and creation from a diverse mix of personnel, regardless of sex, race, religion or nationality, OMRON conducts diversity training programs and undertakes several initiatives aimed at creating equal opportunity among its 35,000 employees.
On that end, OMRON has launched its global training program titled, “Women’s Leadership Training.” Currently conducted across its offices across the Americas, the training is not focused on just practical aspects such as presentation skills and in-office behavior. The training program provides the opportunity for new female managers to optimize their work-life balance as well as laying out a roadmap for their respective, individual careers. The program, which started in 2017 with a scale of 30 female employees, is projected to grow to 250 in the current year.
Driving forward, OMRON will continue to operate by its motto of “Sensing & Control + Think” and pioneer solutions for a number of businesses including industrial automation, electronic and mechanical components, automotive electronic components, social systems, solutions and service, healthcare, and environment solutions, among others. Founded in 1933, OMRON currently provides products and services in 117 countries.
Under the leadership of President and CEO Yoshihito Yamada, OMRON is in prime position to ramp up its efforts to advance the manufacturing industry.

I agree We use cookies on this website to enhance your user experience. By clicking any link on this page you are giving your consent for us to set cookies. More info