THANK YOU FOR SUBSCRIBING

BISTel: Leading the Evolution toward Smart Manufacturing

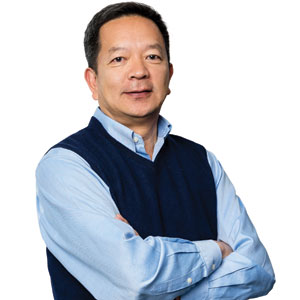
BISTel in its quest to deliver enterprise-wide productivity solutions for the manufacturing industry brings a suite of products designed to help customers detect issues in their systems and equipment, analyze their root cause, and prevent failures. The company provides a suite of equipment engineering system (EES) solutions on a single platform that focuses on equipment health and diagnostics, ranging from real-time fault detection, run-to-run optimization, recipe management to preventive maintenance. Performing complex analysis on the plethora of manufacturing data is BISTel’s eDataLyzer (eDL) advanced analytic platform which features the company’s advanced analytic engines including Map Analyzer, IntelliMine, and Trace Analyzer.
It allows customers to pinpoint root-causes of production issues quickly and accurately. The eDL analytic suite provides users the ability to sort failure/ yield patterns, make correlation, and analyze any type of manufacturing data. Traditionally, root cause analysis for a single production issue could take days or weeks and would involve multiple domain resources, however eDL accomplishes the same in minutes or hours with a single engineer.
In high-tech manufacturing, achieving maximum equipment utilization and optimizing throughput are critical components for calculating the overall return on investment due to the complexity of the manufacturing process. BISTel’s Chamber Matching (CM) solution allows engineers to effortlessly and quickly compare performance of a fleet of equipments. The solution automatically identifies the highest performing piece of equipment (the reference), and simultaneously compares this reference to all other equipments in the fleet to help engineers maximize performance of their entire fleet. Further, BISTel’s Dynamic Fault Detection (DFD), a next-generation fault detection solution with full trace analysis capability helps in early detection of potential production issues. It accurately and comprehensively detects any process abnormalities in real time, without the need to set up control limits. It greatly reduces the time to deploy the fault detection system and speeds up production quality and yield.
“Our vision is to provide a comprehensive solution suite to enable our customers to achieve total smart manufacturing,” states Tom Ho, President, BISTel America. The plan is to achieve this in different phases: first, by developing smart solutions for specific applications including equipment matching and adaptive fault detection. The next step involves leveraging BISTel’s smart solutions to create an automated manufacturing system that can learn, adapt, and predict on its own. Finally, the various smart manufacturing systems interact with other systems such as ERP to create an enterprise that operates autonomously and intelligently, reducing lag time and human errors.
BISTel has already initiated the release of its next-generation “Manufacturing Intelligence solutions such as Health Monitoring and Prediction (HMP).” HMP leverages machine learning and artificial intelligence to monitor equipment in real-time, provide early warnings of impending failures, and predict remaining useful life (RUL) of the equipment. Engineers can now access health information on their equipment anytime and know exactly when to schedule maintenance based on the RUL information. This helps to reduce unexpected downtime and effectively maximize equipment utilization. With new technologies continuing to be a part of BISTel’s roadmap, the company strives to help customers on their journey toward smart manufacturing.
In high-tech manufacturing, achieving maximum equipment utilization and optimizing throughput are critical components for calculating the overall return on investment due to the complexity of the manufacturing process. BISTel’s Chamber Matching (CM) solution allows engineers to effortlessly and quickly compare performance of a fleet of equipments. The solution automatically identifies the highest performing piece of equipment (the reference), and simultaneously compares this reference to all other equipments in the fleet to help engineers maximize performance of their entire fleet. Further, BISTel’s Dynamic Fault Detection (DFD), a next-generation fault detection solution with full trace analysis capability helps in early detection of potential production issues. It accurately and comprehensively detects any process abnormalities in real time, without the need to set up control limits. It greatly reduces the time to deploy the fault detection system and speeds up production quality and yield.
“Our vision is to provide a comprehensive solution suite to enable our customers to achieve total smart manufacturing,” states Tom Ho, President, BISTel America. The plan is to achieve this in different phases: first, by developing smart solutions for specific applications including equipment matching and adaptive fault detection. The next step involves leveraging BISTel’s smart solutions to create an automated manufacturing system that can learn, adapt, and predict on its own. Finally, the various smart manufacturing systems interact with other systems such as ERP to create an enterprise that operates autonomously and intelligently, reducing lag time and human errors.
BISTel has already initiated the release of its next-generation “Manufacturing Intelligence solutions such as Health Monitoring and Prediction (HMP).” HMP leverages machine learning and artificial intelligence to monitor equipment in real-time, provide early warnings of impending failures, and predict remaining useful life (RUL) of the equipment. Engineers can now access health information on their equipment anytime and know exactly when to schedule maintenance based on the RUL information. This helps to reduce unexpected downtime and effectively maximize equipment utilization. With new technologies continuing to be a part of BISTel’s roadmap, the company strives to help customers on their journey toward smart manufacturing.

I agree We use cookies on this website to enhance your user experience. By clicking any link on this page you are giving your consent for us to set cookies. More info